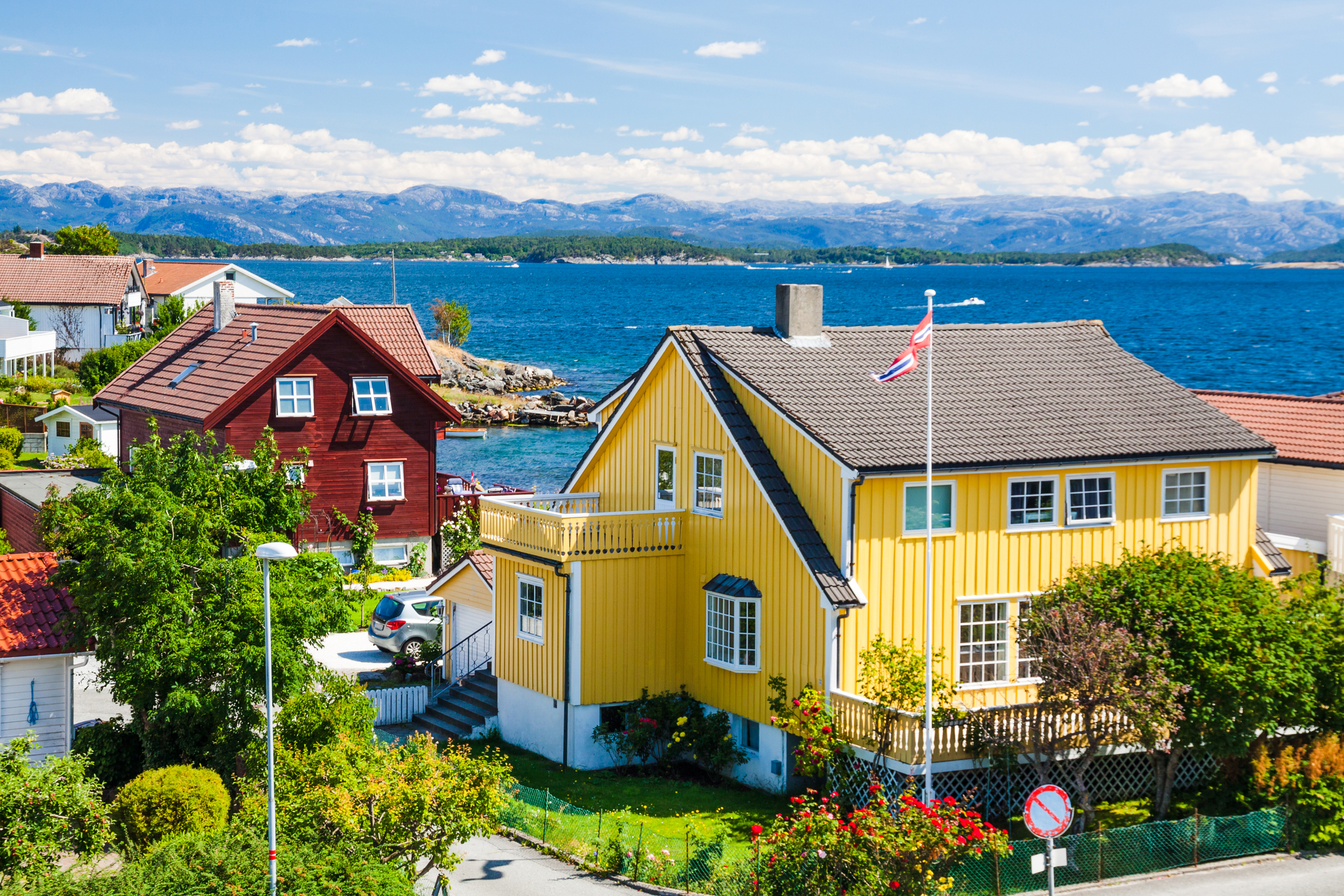
Receptacles over Baseboard Heaters - A Fire Waiting to Happen
I took a trip down to Boise a couple of weekends ago. Just because I was off the job doesn’t mean the eyeballs quit working. We stayed at a converted residence but it was pretty clear that not all the work done to upgrade the traveler’s spaces meets the current safety standards.
In this case, it was a baseboard heater with a receptacle located immediately above it. This is a pretty common finding in older homes in Pullman and Clarkston, but it also represents a fire and shock hazard.
Older Wiring in Existing Homes
You can add cautious concern about older wiring in existing homes to the list of things that your home inspector needs to be focused on.
Despite the house building boom that's in progress, most people are still buying used homes. The National Association of Realtors doesn't like that term, preferring 'existing homes'. Regardless of the terminology, 5,540,000 previously-occupied (how's that for invention!) homes sold in 2016. New home construction added 563,000 homes, less than ten percent of the total.
With these older homes comes some interesting issues and the wiring is moving up the list for houses constructed during the Baby Boom (1946-1965-ish). Much of this wiring iscopper with a rubberized thermoset insulative cover with both the hot and neutral cloth-wrapped. Usually, there is no ground wire. For this article, I am focusing on the properties of the wire and won't be discussing the ungrounded nature of it. Another article, another time . . .
New wiring spliced onto the existing cloth-wrapped wiring.
While this wiring has been remarkably stable, old-age is catching up to it. Specifically, the thermoset coating is beginning to fail. The rubbers are becoming brittle with time. This is most common in the houses built before 1960, but the Residential Electrical Systems Aging Research Project - Final Report was published in 2008, making even this data a decade old.
I periodically hire electricians, plumbers, and such to spend an hour with me, going over the trends that they see in their industries. I recently did this with Jess Izzo of Omega Electric in Pullman, Washington. I asked questions, Jess talked, and I ended up with a page full of notes to apply to home inspections.
According to Jess, the electricians are seeing a greater incidence of wiring failures. When they are called into a home to do even modest repairs or upgrades, they are noting cracked insulation on the wiring. The current fix for this is to re-wrap the wiring. Jess stated that he does this before he begins on the device replacement to limit the amount of deterioration that occurs.
From a home inspector perspective, this means I need to be aware of homeowners who may have installed new lights, receptacles, and devices without being aware of the fragility of the thermoset.
While this wiring is still serviceable and even though homeowners are permitted to perform their own repairs on their personal residence, my advice to home buyers will be to hire an electrician for any work that needs to be done. A receptacle replacement itself is reasonably easy, but the risk of causing unintended damage outweighs the ease.
Ufer Ground for New Construction
The term ufer ground is the old fashioned way to call out what the code book calls a concrete-encased grounding electrode. You probably don't know it but most new homes in the Pullman and Moscow areas are being built with a Ufer ground. First, let's have a short history lesson. In World War II, the American forces, specifically the U.S. Army, needed a system to ground bomb storage facilities in Arizona and Nevada. One problem with both of those areas is that they are extremely dry and the soil was a very poor conductor. For obvious reasons, the Army did not want excessive charges to build up around the bomb dumps. The existing means - long copper rods - would take a critical war material our of circulation and was very expensive.
Fixing this problem was Herbert G. Ufer. A sharp individual, he discovered that the foundations, made of concrete, were more conductive than many types of soil. He devised a system by which a rod was inserted into the foundation and tied to the electrical panel.
Moving on....
The concrete encased grounding electrode used in our region for residential construction is a 20 foot length of #4 rebar (1/2 inch steel) with a projection from the top of the foundation wall at a easy location to make the connection to the grounding electrode - the actual wire from the panel.
The old means - there were two - of grounding proved to be less effective in Pullman and Moscow due to better knowledge and a change in building material.
The early means of grounding was to attach the grounding electrode to the metal plumbing system where the main entered the home. Now that we use non-metallic materials for our plumbing supplies, this option isn't available.
The other way was to use driven ground rods. Unfortunately, these were less proficient at distributing energy and were often damaged at the clamps that held the wire to the rod.
How to determine if you have a Ufer Ground? Look inside the home under the electrical panel. What you are trying to find is a blank electrical box cover plate. If you have one and can not find a ground rod outside, there is a good chance that you have a ufer ground. The plate is there, by the way, in case you do have a major electrical event and the connection to the rod needs to be checked for damage.
Now a word of warning - nothing ever comes without a downside. Ufer grounds have been known, under certain conditions, to cause damage to the foundation in a lightning strike. If the concrete holds too much moisture, that water will flash off to steam and the expansion of the steam cracks the concrete.
Make sure that you keep your gutters in good shape and, when you water the lawn, make sure you're not watering the house, too. It's not good for the house and it can be a problem - not a high probability one, admittedly, but possible - for your ufer ground system.
Washington State License #215
Former SBCC Member, Former Chairman State Home Inspector Advisory Licensing Board.