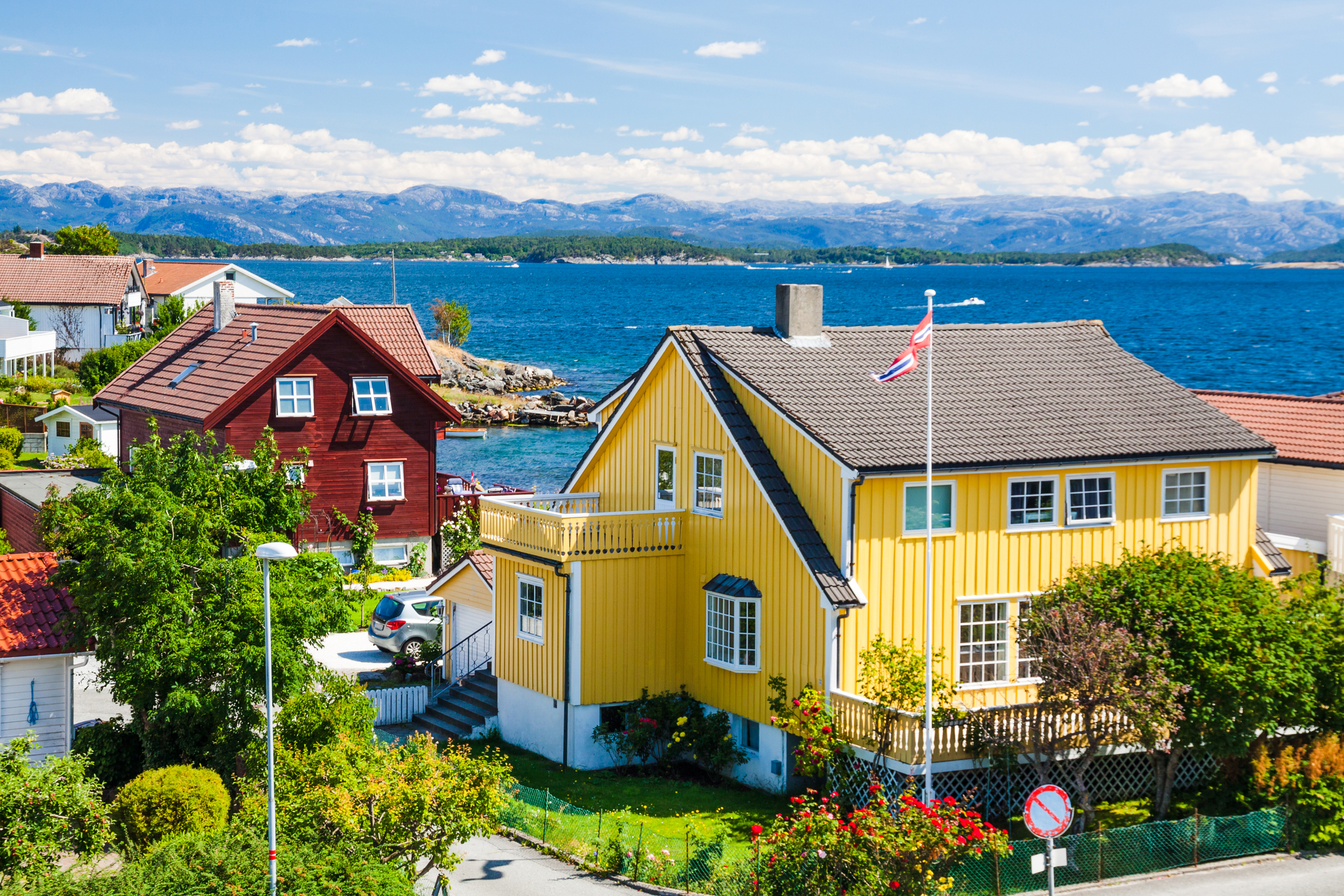
Sewer Scoping and Home Inspections
Sewer Scoping and Home Inspections
Having a sewer scope done while the home inspector completes his works looks like a no-brainer. After all, the home inspector will not be checking the plumbing under the slab of the house or underground.
I agree. That's why I recommend professionals to do sewer line inspections with professional grade equipment.
Why don't I do it myself? All the home inspector organizations say it is a great add-on that will make me a lot of money.
The truth is that I did offer sewer scoping with home inspections in Moscow and Pullman and Lewiston. But, the same as with home inspections, a person who does six a day is going to be far better at sewer scoping, finding problems before their YOUR problem, than a home inspector who does it on an occasional basis.
Also, in the State of Washington, a contractor's license from Labor and Industries is required to perform sewer scoping. I let my lapse when I stop sewer scoping. None of the inspectors in Pullman or Clarkston carry the license, either.
So, I recommend the following companies for sewer scoping here:
All will do a great job for you. They're pros in their field.
And, if you need a pro in the home inspection field, please give me a call. I'd be delighted to be of service.
How To Incorrectly Install the Temperature Pressure Relief Valve - Or Boom Waiting to Happen
With any luck, when I do a home inspection, I get to stay nice and bored. That doesn’t happen as often as I would like unfortunately. Part of the boredom should come from verifying mundane details that nobody would ever get wrong.
Ha. Just kidding.
In this case, the mundane detail is the temperature pressure relief valve. These devices have been required equipment since the 1960s. Their purpose is to act as the last fail-safe on the water heater tank. The tank is a welded steel enclosure which means that it doesn’t structurally fail easily. It takes a considerable amount of energy to force it into failure. Or time, but that is more for leaks. Here I am concerned with a sudden catastrophic failure.
Most people would pay more attention to their water heater if they knew they were living with a bomb. Think I’m joking? Go check out this video from Mythbusters. Don’t worry, I’ll wait.
Welcome back! Impressive, wasn’t it.
Please note that they deliberately disabled the TPR safety to get the tank to go boom. In my job, I don’t need to assume intentional action or malice. Ascribing mistakes to simple silliness or ineptitude works just as well.
In the video below, a TPR vale is installed. Sadly, it is not installed correctly and has created the potential to turn the water heater into a house killer. Maybe a people killer, too. Bad news, that. It is, however, easily fixable.
The hottest water temperature I’ve ever check was 189 degrees on an old National Steel water heater from the fifties with no TPR valve. I practically begged the client to replace it.
The Hose Isn't the Clue - When to Worry about Your Sewer Line
Home inspections are a neat way to make a living. I love the puzzle-solving aspect involved in the process. Today, I was in a 1970s vintage home that made me stop and go '“Hmmmm.”
Why? Because of an odd little circle of dirt. It was around a floor drain and might as well as have announced “Flood!” A small one, but since I hate water outside the plumbing, it made me dig deeper.
I ran water in three bathrooms and the kitchen for an hour to replicate the flood event. No bueno, no flood. It wasn’t for a lack of trying.
Still, I advised my clients to get a sewer scope done on the main waste line. Something happened and I’d rather they spend a few extra dollars making sure the drain is good than tell them that I did my best but what’s underground is not my responsibility only to have the system blow up six months after they move in.
The standards of practice define what I must look at and what’s within my scope, but it shouldn’t prevent me from using my brain.
Don't Let Your Hose Cost You Big Money and Aggravation
Winter’s coming. You know what that means?
I’m going to start finding frozen pipes. Bummer. Here’s a quick, easy way to avoid the most common source for broken pipes.
New Requirements for Water Heaters
With the adoption of the newest plumbing codes, the issue of strapping water heaters against earthquakes just went nation-wide. Mind you, the earthquake risk did not. Whitman County is still a Seismic Zone B, as is Asotin County.
The relevant code is the UPC 507.2 and was adopted by the State Building Code Council. The full text reads:
507.2 Seismic Provisions. Water heaters shall be
anchored or strapped to resist horizontal displacement
due to earthquake motion. Strappings shall be at points
within the upper one-third and lower one-third of its
vertical dimensions. At the lower point, a distance of not
less than four (4) inches (102 mm) shall be maintained
from the controls to the strapping.
This does not (I think) mandate repairs. In my reports, I will be adding the strapping as line and recommending it as an upgrade for older water heaters. For installations after July 1st, a lack of strapping will be listed as a repair item.
Avoiding Frozen Pipes
The Washington Post has an article on what to do if your pipes freeze. Not a current worry here, but worth filing away for the future.
Here's some of the advice that I left:
Let's throw some extra pointers out there . . .
1. Leave the sink base cabinets open to allow better air flow, especially in older homes with poor wall insulation.
2. Make sure you don't have any hoses hooked up outside and that the hose bibs are protected with insulating covers.
3. If your house is vacant, call a friend/realtor/somebody to check on it and make sure the heat is on.
4. If you have a crawlspace, close the vents for the time being. Ideally, any plumbing line in the space should be insulated.
5. If you have a basement look for water lines that are in contact with concrete. Put a piece of insulating material, even some rubber, behind the lines to get them off the walls and fill the air gap. Pay attention to the laundry lines in old houses.
6. Add portable electric heat to spaces where pipes are subject to freezing. Use as little heat as you can and make sure there are no combustibles nearby.
Better to go to overkill on precautions than to deal with a flood.
Testing Water Temperature during the Home Inspection
As part of my home inspections, I test the water temperature at a minimum of one fixture, and sometimes, more. The State of Washington Standards of Practice states that the Inspector will report "Whether or not the water temperature was tested and state that the generally accepted safe water temperature is one hundred twenty degrees Fahrenheit."
Most inspectors simply report the generally safe accepted level and let it go. I don't for reasons that I'll cover here in a moment. First, the following will give you a sense for how hot water can injury. Note that these are for average adults, not small children or the very elderly.
- Water at 100 degF or below is unlikely to scald an adult occupant at any exposure time.
- Water at 120 degF for 5 minutes can cause 2nd & 3rd degree burns on adult skin
- Water at 130 degF for 30 seconds can cause 2nd & 3rd degree burns on adult skin
- Water at 140 degF for 5 seconds can cause 2nd & 3rd degree burns on adult skin
- Water at 150 degF for 1.5 seconds can cause 2nd & 3rd degree burns on adult skin
- Water at 160 degF for .5 seconds can cause 2nd & 3rd degree burns on adult skin
My record for water temperatures, actually measured in a home in Moscow, was 179 degF, hot enough to make coffee with. 150 degF is not all that unusual.
The reason all this came to mind is a report of Legionnaire's Disease in the Bronx. For those unfamiliar with the disease, it is bacterial in nature and a particularly nasty form of pneumonia. It is water-borne but, to infect, it needs to be inhaled. Think humidifiers or showers where the bacteria in the water is atomized to particles that can be breathed.
The types of systems most likely to create ideal conditions? Cribbing from OSHA, "Warm, stagnant water provides ideal conditions for growth. At temperatures between 20°C-50°C (68°-122°F) the organism can multiply. Temperatures of 32°C-40°C (90°-105°F) are ideal for growth. Rust (iron), scale, and the presence of other microorganisms can also promote the growth of LDB."
Sounds a lot like the well water we have here, conveniently heated to nearly ideal conditions for growth inside our water heaters.
Per OSHA, "Maintain domestic water heaters at 60°C (140°F). The temperature of the water should be 50°C (122°F) or higher at the faucet."
That's why I test the temperature and why, if the client is attending the inspection, we discuss the temperature. I don't call out high water temps as a safety hazard until I measure 130 degF. Even then, the discussion starts first with a question about who will be living in the home with the client.
I explain the state standard, which is based on manufacturer liability standards, as well as energy conservation standards. Then I explain the third leg of the risk triangle, bacteria control.
The reason that I might consider testing at more than one location in the home is that the newer faucets, especially for tubs and showers, have tempering valves. That is, the valve blends cold into the hot to moderate the temperature to safer levels. The place to get the most accurate reading on the output temperature of the water heater is usually at the utility sink since the hot and cold water controls separate.
If I get a low reading but a very fast rise on the temperature, I look for additional test points to confirm my reading. I don't want to inform the client that the temperature is under 120 degF if the test point is subject to tempering.
Depending on their particular circumstances, the clients may wish to leave the water temperature at a higher level than the standard. The point is to ensure that they are well informed on both the pros and cons of setting the water temperature for the home.
Residential Fire Sprinkler Systems
One advantage of being appointed to the State Building Code Council is the introduction to new knowledge. Yes, I know, that sounds incredibly nerdy. Welcome to the world of home inspection. In the model building codes published by the International Code Council, fire suppression systems have been required in commercial settings for decades. The introduction of sprinklers into the home has been much slower. As of now, only 4.6 percent of occupied homes (including multi-family residences) are equipped with the systems but that represents a substantial improvement. The pace of installations has increased as states begin adopting the model code and incorporating it into the new building standards.
Now for the fun stats on dying in a fire. 85 percent of all fire-related deaths occur in the home. You cut our risk by a third if you have smoke detectors. In acknowledgment of human nature, the odds improve to fifty percent if the smoke detectors are working. (Now would be a fine time to check the batteries in your detectors.)
Your risk drops by 80 percent if you have sprinklers installed.
Despite the statistics, the public resists the idea of installing sprinklers. Two factors play into the resistance. The first is cost. Costs continue to drop which is the good news. The bad news is that they still are not inexpensive. The estimated cost in new construction is $1.35 per square foot of sprinklered space.
The second issue is the misinformation regarding the systems. You might be shocked to discover that modern television has fibbed a bit about sprinklers. When a fire sets off the spray nozzles, they don't all go off - just the one that is needed to put out the fire, which it usually manages to do so before the fire department can even get to the home.
If you've ever seen a home after the fire department hosed the place, one sprinkler makes far less a mess. That is, in fact, how many heads activate in a fire - one. The property loss is usually about 70 percent less with sprinklers, a positive feature for insurance companies.
Another fear is a false discharge. The new systems are designed to prevent that by not activating until a higher temperature is identified. Depending on the system, the activation temperatures is usually150 degrees. At that temperature, the glass bulb that activates the individual head to put out the fire.
I had the opportunity to watch a demo put on a by the Washington Fire Sprinkler Coalition. They tested a system under controlled conditions and the portable system worked beautifully. The fire was extinguished within seconds.
According to the men running the demonstration, this is typical of the response time of the modern sprinklers. If you have these in your home, you can be more confident that, in the event of a fire, you are much more likely to avoid tragedy.
Underground Oil Tanks
In the last month or so, I've run into a ton of misinformation regarding underground oil tanks. Early in the month, at the ASHI-WW training session, I got involved in a conversation with inspectors from western Washington. Apparently, there are companies on the west side that will remove the tanks and perform mitigation, for $5,000-$10,000. Discovery of an oil tank on a property there often kills the deal in a dispute about who mitigates the problem. By the way, keep in mind the size of those tanks. It's actually an important number. The second occurrence was on the Idaho side of the line. Similar deal, oil tank was present (and in use with a converted coal-burner now acting as the oil-fired boiler.) The agent was concerned because, in her investigation she had contacted the City of Moscow, who referred her to the Idaho Department of Environmental Quality (DEQ) and said that there were the folks that managed the decommissioning of underground oil tanks. Folks, any time the DEQ gets involved the price tag goes up. It's the nature of what they do. In this case though, the City of Moscow gave bad advice, the same bad advice that the Washington home inspectors have been getting.
First, a little history . . . .
Above Ground and Underground Oil Tanks
These tanks store the oil that is - or was - used to fire the furnace in the house. Depending on the region, these tanks could be above or below ground. Above ground tanks made for easier monitoring but the home heating oil has a tendency to 'jell' in extreme cold so a means of keeping the oil liquid and flowing was a necessity. The above ground tanks were easy to deal with when the homeowner eventually converted from oil to gas or electric heating. Empty them out and haul them away.
Underground oil tanks poses separate issues.
There are thousands of unused underground residential heating oil tanks in existence and many still contain heating oil. These tanks are typically 300 to 500 gallons in size and made of 12 gauge steel (about 1/8 inch thick). They average about 30 years before corrosion makes them prone to leaking, but the life of individual tanks varies widely depending on the properties of the surrounding soil.
These tanks were often just abandoned in place, the only clues that they still exist, a copper feed line, or a breather vent, or the fill cap. Most of the tank, ranging in size from 200 to 500 gallons, are hidden from view. Even the pieces above the ground on the exterior - the fill pipe and breather vent - might be obscured by vegetation. In short, they can be really difficult to identify.
Under Washington State regulations, the home inspector is required to "Report any evidence that indicates the possible presence of an underground storage tank."
Myths
Myth 1 - The EPA regulates underground storage tanks so homeowners need to follow their regulations
This is the source of most of the confusion. Remember when I said to keep the tank sizes in mind above? Yep, they're important. The EPA regulates fuel storage tanks that are larger than 1100 gallons. Home heating oil tanks are specifically excluded statutorily from EPA regulation (with a large caveat that once the tank leaks and reaches a body of water, you've got a huge problem.) The EPA site has this statement - "Tanks used for the storage of heating oil for consumptive use on the premises where stored are excluded from federal UST regulations. However, state or local regulatory agencies may regulate these tanks."
Myth 2 - Washington State, Idaho State, Regulate Underground Storage Tanks
They do - in exactly the same way the EPA does. Again, the threshold for both states for regulating UST's is 1100 gallons. The State of Washington has a handy little flyer that will lead you through the process. Quoting Washington State, "Neither the federal government nor Washington State regulates the use or operation of residential heating oil tanks."
Since I live on the border between two states, I get to check everything twice. Sure enough, Idaho has a similar flyer, a little longer (head for page 6 - that's where you'll find the stuff for homeowners) that expressly states. "Some kinds of USTs are not covered by these regulations: Farm and residential tanks of 1,100 gallons or less capacity holding motor fuel used for noncommercial purposes."
Myth 3- A leaking oil tank is a huge liability to the homeowner
This one is partially true but only under certain circumstances. I'm going to use the Washington State Department of Ecology answer for this one as it is the most straight-forward. You are not required to report minor spills or leaks. They specifically defined a minor spill as ". . . those that affect only the soil near the tank."
The point where liability becomes a major concern is when one of two events occur: first, the spill contaminates a water source, whether it is a natural body of water such as a stream, river, lake, or well; and, second, if the spill impacts a neighboring property and contaminates it. There are ways to manage these risks if you have underground oil tanks on your property. Both states maintain programs to assist homeowners with insurance that would likely be impossible to obtain otherwise.
Washington State has an insurance program for homeowners - it's free but not transferrable. Go to the Pollution Liability Insurance Agency to get the details.
Idaho has a similar program but it's not free. There is a $25 annual fee to access the services at the Idaho Petroleum Storage Tank Fund
Myth 4- My underground oil tank is not in use. I have to remove it.
Maybe, but probably not.
The places to check on exactly how you are obligated to handle a tank decommissioning are the local building department or the Fire Marshall's office. I'd contact the Fire Marshall first as they usually have a better idea of the local regulations than the building departments, especially in smaller locales.
You are required, if the tank has been out of use for more than 1 year, to decommission it.
You have two options for decommissioning. The first is removal and this is by far the most expensive option. The second is to fill and abandon in place. Let's look at both.
Removing the Tank
First, understand that this is generally not required by law. Most municipalities realize the expense involved. Also, tanks that were accessible in the past may be hard to reach with the necessary heavy equipment now that the neighborhood has filled in and the landscaping has matured.
Both state environmental department - DEQ in Idaho, Ecology in Washington - recommend this option. Their argument is that it is easier to identify leaks this way (which they will then likely make you mitigate at your cost!) and that some mortgage lenders or insurers will want the potential hazard addressed. On the first point, they have a vested interest in the cleanup process.
The second is a case by case process. A properly decommissioned tank that has been fully documented to meet the applicable regulations probably will not trigger a problem for you in the loan process. The key is the documentation.
Leaving the Tank in Place
This is a popular method to handling oil tank issues due to the reduced cost.
First, a warning. You can't just leave the tank and not do anything. Old tank will rust and they are subject to floating out of the ground in areas with high water table and to collapsing from rust. Usually that collapsing is encouraged by an unsuspecting soon-to-be emergency room visitor when they walk or play above it.
Decommissioning underground oil tanks requires a few steps. The early steps are the same for removing the tank.
- Pump all remaining oil from your tank
- Clean out any sludge in the bottom of the tank.
- Remove or cap all lines.
Here things separate. With removal, you uncover, lift out, and check for contamination before backfilling.
Abandoning in place requires a non-compressible, leak-proof fill material. Commonly, we'll see a weak cement slurry, sand, or foam. Personally, I favor the weak sand slurry. It's the same material that many utilities use to backfill trenches for gas line, fiber optics, etc.
Before You Begin
Whichever option you choose, make sure you check with the local jurisdictions first. You will almost certainly need to obtain a permit in a larger city. Smaller cities and towns may not require it but check anyway. You may discover that they have useful information regarding soil structures and local hazards that will be helpful in making a rational decision.
Hire a company that specializes in underground oil tanks. Bob the local handyman is probably not your best option for this project. Check to make sure that they carry the appropriate licenses and that they are insured, both for the tank services they are providing and also for general liability for any damage they might accidently cause.
After You're Done
Maintain a paper trail of all the work that was done, by whom, in a file. To document decommissioning of the tank, the property owner should retain a copy of the any reporting forms used by the local municipality, any permits, as well as all receipts, certifications (including those of the contractor that you wisely verified), and written materials associated with the project.
Make a copy of the file for yourself, and when you place the home on the market, a copy for your Realtor.
Keep Your Water Lines from Freezing!
Yesterday morning, I had the first hard frost of the season on my truck which means it's time again to talk about how to keep your water lines from freezing.
Hose Bibs
I have a comment that is embedded in my report that I use all winter:
In winter weather, it is a good idea to remove hoses from the bibs to prevent damage from freezing.
It is such a common item that we don't even notice it. The hose is still attached to the bib - more often than not, it seems, the hose bib is a frost-free. People like frost-free bibs for good reason - having a pipe freeze and break inside a wall is a major pain. The problem is that a frost-free valve doesn't work if the hose is attached and has water in it.
The frost-free valves work by having the actual shutoff inside the mechanism inside the wall, not at the handle on the outside of the home like the old 1950's style faucets. When you turn the valve off, the remaining water drains from the spigot so that it can't freeze. A hose prevents the draining. If the water is in the line and freezes, it expands and your pipe can rupture.
Make sure you remove any splitters or quick releases - these present the same problems. Also, make sure you don't have a slow leak as the water drips can freeze up the opening acting as a cap.
I recommend putting on covers to the hose bibs for a bit of extra protection. Will the inspector remove it - probably not, in my experience.
Many older homes that lack frost-free valves have shut-offs inside the house. If yours does, use it and then open the valve on the outside. I recommend covers on all non-frost-free valves.
Interior Plumbing
If you are living in the home while it is on the market, most of this is not going to be an issue for you but if you've already moved and the house is vacant but you want the water on, I want to remind you to do a couple of things that will keep the plumbing in safe conditions.
First, leave the heat on. It doesn't have to feel like the Bahamas inside, but you should keep the thermostat set to 55 degrees or higher. Leave all the cabinet doors open below the sinks to allow heat to get to the pipes. If you are not going to leave the heat on at all, you have to fully winterize the home. I will talk about winterization in another post next week . . .
Second, make a decision on whether you want to turn the water off to the home. If you turn it off, crack open the valves and drain the system as best you can. Leave a couple of the faucets open to allow the pressures to stabilize.
If you leave it on, ask your Realtor to check in on your property at least weekly. Some inspectors will also perform this service, so ask around. What you want from them is a visual inspection of the plumbing. In bitterly cold conditions, these visits should be done daily. It may cost a bit on money but I can promise you that the expense is less than that of spraying water and a flooded house.
In extreme conditions, the hot and cold water should be left on a trickle. As anyone who has paid attention to a river realizes, moving water is less likely to freeze.
Plumbing pipes at exterior walls, in unheated basements, and the crawlspace are most in danger. You may need additional heat or a heat tape in these locations. Any plumbing that is in unheated spaces should be insulated but, by the time you move out, it's probably too late unless you want to spend the extra money for your buyer. You should know that Washington State Standards of Practice mandate that we identify these in the report though we are required to recommend upgrading - for now, at least.
Don't forget the fixtures - and the water heater!
The toilet reservoir holds up to three gallons of water. Having that water turn into a block of ice - or worse, having the water heater freeze - can be disastrous. The picture to the right is from an inspection I did two winters ago. The seller eventually spent thousands of dollars to make the necessary repairs.
If the heat is off, it is imperative that you, at a minimum, drain the toilets. If you turn the water heater off, drain it as well.
And, for what it is worth, the agent had recommended a full winterization. It was excellent advice and would have saved this seller a goodly chunk of cash.
It would have also kept the buyer from freaking out - and to be clear, this inspector is not a big fan of plumbing problems. They often end up more complex than first realized and always seem to involve a combination of multiple trips to the hardware store, bad language, and a good plumber.
A good agent is worth his or her weight in gold - please listen to them if they say you should winterize to keep your water lines from freezing. And follow the other steps above even if you are occupying the home. Especially those pesky hose bibs.
Video Sewer Scope and Old Pipes
If you have an older house, getting the someone to do a video sewer scope inspection can possibly save you thousands. The issue that I run into on a home inspection is that I do a visual non-invasive inspection (mostly) and the sewer line is buried under ground making it outside the scope of what I do.
Based on the age of the home, I can make some educated guesses on what material - ABS, cast iron, concrete, Orangeburg - you may have connecting your home to the city sewer or to the septic tank. What I have no way of telling you is what condition those pipes may be in.
When I have some concerns, I recommend you to a professional who has the equipment - a sewer scope which is a camera on a long flexible lead that gets pushed down the sewer line, sending back images to a video recording system.
Ideally, this operator will send the probe to the connection with the main sewer line or septic tank and report back what the material is and that it is in good condition. Unfortunately, as plumbing pipes reach the end of life period - and this is occurring more often with the post-WWII homes approaching 70 years old - we're seeing more failures.
The failures tend to aggregate into two categories. The first, material related, is simple degradation of the pipe. Orangeburg pipe - basically a toilet paper roll impregnated with tar - simply falls apart. Cast iron has rust issues.
The second category deals with time and the effects on the conditions around the pipe. One example is a failure of compaction in the soil that causes the pipe to shift or even break. This can be a problem with modern drainage piping - the lines often will develop sags that restrict flow. Another one, a particular problem in older neighborhoods are the wonderful mature trees.
I had a beautiful jacaranda tree in my front yard when I lived in Southern California. One of the reasons it was so spectacular was that it had a steady source of nutrients - my sewer. Trees are opportunistic and this one found all the joints in the clay piping and invaded at the seams where each hub piece was joined.
I bought that house before video sewer scope technology matured so I didn't get the advanced warming - the total tab was nearly $5,000 in repairs. Now that the technology is here, I recommend it to clients with older homes.
The actual wording that I use is " It is not unusual for older homes to begin to have problems with the waste drainage system. These systems are not readily visible but can be imaged using a video sewer scope system. Recommend having a video camera line inspection for potential blockages in the main sewer line."
It's up tot he client to make the call obviously - but it awfully cheap peace of mind.
Low Water Pressure for the Whole House
Turning on the shower and discovering that you have such low water pressure that you can't get the shampoo out of your hair is frustrating - especially if, like my daughters, you have rather abundant hair. The good news is that it is relatively rare, much rarer than high water pressure.
The cause can be fixture specific, system specific (all the hot water lines are affected) or, in the case I had last week, affecting the whole house.
Testing for water pressure is not part of the Washington State Standards of Practice for home inspectors. Still, it isn't hard to do and can give the inspector clues on conditions inside the home.
In the photo to the side, you can see the gauge is reading about 32 PSI (pounds per square inch.) The water pressure I expect to see in normal residential housing is 40-80 PSI so this was definitely on the low side. A quick check inside allowed me to verify that nobody was using water and pulling the pressure down.
There are a half dozen considerations that must be taken into account when I see a reading like this. The age of the home is the first. If this were an older home, I may be looking at a main supply line that is corroding/failing.
Likewise, the individual line to the bib might be failing so determining the material is important - some materials degrade faster than others.
The answer I don't want to arrive at is that the municipal supply is that low. Without a booster system, which isn't horribly expensive but still an additional cost, what you see is what you'll shower with.
I this case, none of the above applied. The home was relatively new, less than five years old, and had PEX plumbing in good condition. It also had a pressure regulator built into the water supply. The regulators are now required in one of the municipalities that I work in and the plumber's assistant dutifully attached it. However, he forgot to make a simple adjustment to the knob on top.
The buyer was with me, so it took me just a moment to show him how to make the adjustment. Since I do free return visits for my clients, we arranged to adjust it after he took possession. In the end, his low water pressure issue was an easy adjustment rather than a huge potential expense.
PS. For those wondering why I didn't adjust the pressure while I was there, all I can say is that I am a guest in someone's home. I like to leave it the way I found it (unless it is truly dangerous!). It would be like me coming is, deciding I don't like the curtains, and taking them down for ones with little yellow duckies that I like better. As a guest, I should have better manners.
Washington State License #215
Former SBCC Member, Former Chairman State Home Inspector Advisory Licensing Board.