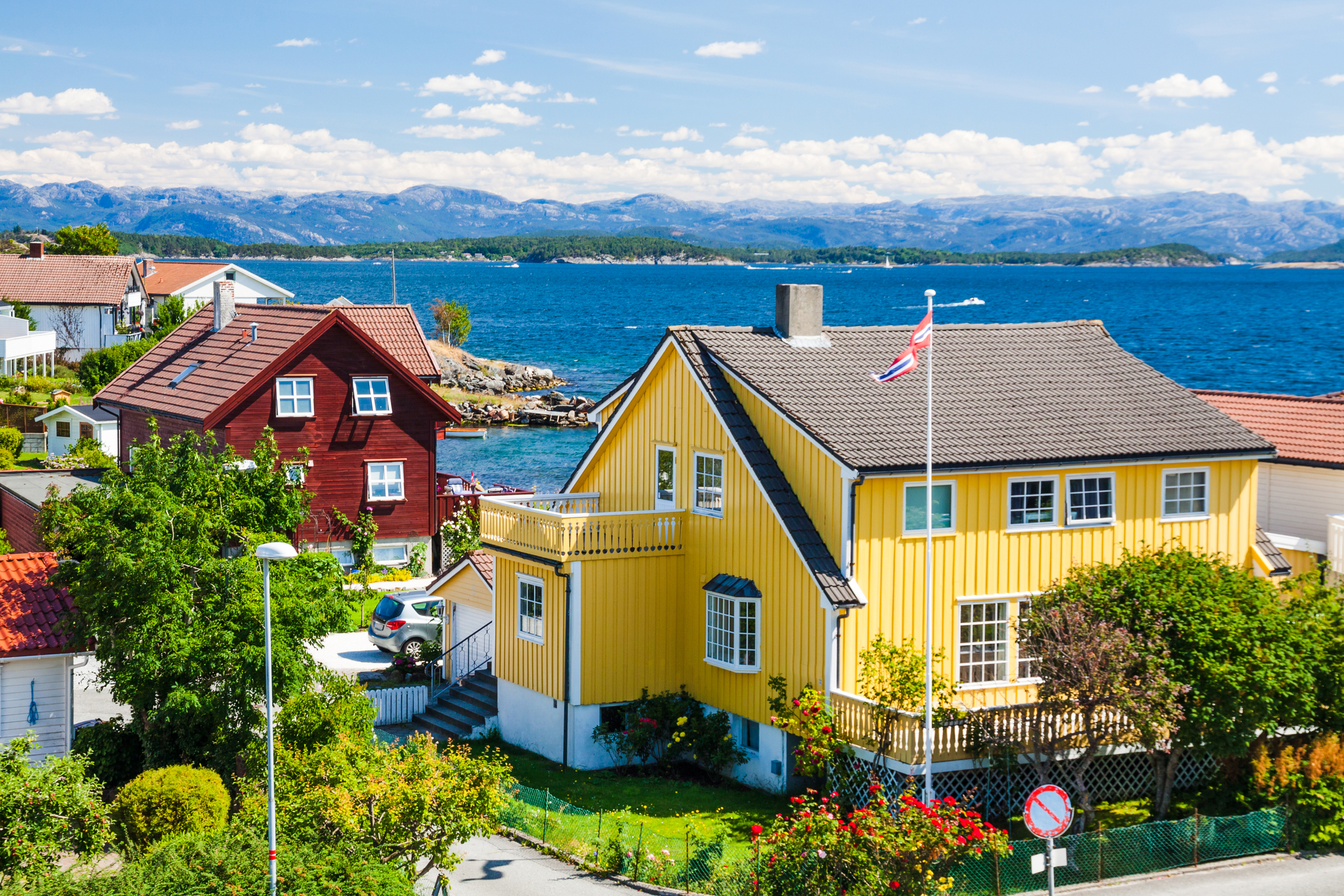
Mold Problem Here?
Mold Problems Here?
I'm seeing a big uptick in requests for mold testing. Interestingly, these are being driven by doctors asking their patients to get tested. Since I am certified in Mold Inspection, I have been getting a number of these referrals.
In each such case where doctors have referred their patients for mold inspection, I have found, through air sampling, surprising levels of mold. Unusually, it is in the exterior samples that I am seeing high numbers which is, obviously, affecting the indoor air quality. Oftentimes, there is NO visible mold present but there have been plenty of mold spores in the air.
And, before anyone thinks “Well, not around here!”, I have done mold testing in Lewiston, Clarkston, Moscow, and Pullman - plus a bunch out of town. Mold is becoming a problem here. Now, that may be the result of a really wet spring - or, it may not. I suspect, but don’t and can’t know, that the past several years of national health issues have impacted the population such that mold that did not affect people previously is now a much more serious concern.
When I am inspecting for mold (NOT included in a home inspection), I am looking for sources of moisture in the entire structure. So, if a client says they have mold in the bathroom, I'm still going to be in all the other rooms, up on the roof, in the attic, and in the crawlspace. I'm also going to be testing surfaces for moistures, testing the air for humidity, and looking under and behind things to find the moisture source.
Sometimes, there just isn't a problem. But, more recently, there has been, from leaking plumbing to a failed dryer vent to water in the crawlspace.
Without testing, we just can't know.
If mold is a concern in your home, I recommend testing. It is a worthwhile investment in your air quality.
Is the Wall Moving - Or is the Floor?
Commercial inspections, known as property condition assessments or PCAs, are a totally different beast from a residential inspection. The standards are very different with commercial work much more focused on the document record and future expenses.
Some problems are common to both residential and commercial work. Foundation issues can obviously affect both and this commercial job was one of the more interesting that I have encountered.
Here, the owner who commissioned the PCA thought that he had a problem with the masonry walls of his building moving so, I naturally started there, examining the exterior foundation and wall assemblies.
Lo and behold, no major movement. There was minor cracking in the mortar joints of the masonry system but nothing that suggested a major failure.
Inside, I had considerable wall separation so I understand why the owner thought the walls were moving. However, I am simply not willing to take things on face value. I investigated further. As it turns out, the exterior walls were plumb. They weren’t moving. That being the case, I turned my attention to the floor. Now, I know, everyone expects the floor to be flat, almost by definition so that seems just silly. I checked anyway. I started tapping on the tile and found hollowness underneath. Time to break out the level again. The floor was not flat.
“Hmmmmm,” he thought.
So, what was going on?
If you look at the this picture, you'll see soil subsidence at the water meter and the fire hydrant. The obvious question to ask is "Do we have a major water problem at the curb?" Is there a leak on the water main? At the hydrant? Maybe the storm gutter for the street is failing?
Now, I'm guessing that you are already ahead of me here. Yes, the building is DOWNHILL from this apparent leak. My best guess was that the water flowed under the building causing a combination of erosion in some areas and soil expansion - clay soils can expand greatly when hydrated. That would explain the hollow areas AND the up-raised edges.
My recommendations? First, find and correct the source of that water. Second, they need an engineer to determine how badly the structure is damaged and how to repair it.
I'm glad the owners called me when they did - water problems such as this NEVER get better with time.
Can You See It?
Can you see it?
Look closely.
Where the walls meet in the corner, in the brown area. See it now?
No?
The wood shingles for the siding have fish-mouthed. And, if you look above the shingles, you'll see the barge rafters at the edge of the roof have separated.
This, unfortunately, gets the home inspector excited and you don't want me excited - you want me bored, bored, bored. Boring houses are good houses.
The gaps above are signals and the place to trace that signal is back to the foundation.
That roof segment is connected to a column connected to a masonry wall that also supports the deck/wraparound veranda. That wall is moving.
I say 'is' because an attempt at repair was made made for the deck - and failed. Newer movement broke a part of the repair.
The mortar for the masonry wall that was cracked has been repaired - and re-cracked.
We have an ongoing, slow-moving problem. It won't fall down tomorrow, but the systems aren't working, they're failing.
What's the solution?
A good structural engineer. I know one and, for stuff like this, I refer him. That's what I did here.
All things are fixable. The only question is who gets to pay. Part of my job is for you to have that question answered up front.
There's nothing worse than you moving in and discovering a year later that you're the deep pocket that will fix a structural failure.
Drone Inspections
After a bit of hard work, I have passed the FAA test to be a Part 107 Remote Pilot. This means that I can legally use drones in the real estate industry. While much of the work will certainly be geared to real estate photography here on the Palouse, the drone that I fly - the DJI Mavic 2 Pro - is a top-of-the-line piece of equipment that can inspect anything from inaccessible roofs to cell towers.
The Mavic is a dream to fly (hat tip to Jess Rainer at Windermene in Pullman for the great advice on drones!) The integrated software and hardware make it possible to take terrific photos and video right out of the box.
Early returns are very encouraging and I’ve already started booking work for the drone. In fact, the first job paid off the insurance for the equipment.
Yes, I carry insurance on the drone and on the drone operation. While there is no legal requirement, it is the prudent option.
I’ll be adding pictures from iconic spots around the Palouse and from the Lewis-Clark Valley every once in a while. I’ll also be building out a separate website for the drone business. While I intend to use the Mavic for inspections, it will be through a separate company.
I’ll keep you posted.
How Old Is This House Again?
I was having a discussion with Chip Kenny, the inspector at Inland Northwest Home Inspections, about a house he was inspecting. The visuals - type of foundation, etc. - didn’t match the age of the home listed in the public sources.
I have run into this three times in the last year. The easiest one was a house listed as a 1965 building in a neighborhood in Pullman that was newer. The house had engineered trusses in the attic and the concrete foundation appeared to more modernly formed. When I opened the electrical panel, I found an inspection card for 1985. That fit much better, and I adjusted my report accordingly.
This structure was listed as a 1953 home - but the framing says 1900-1920.
The nastiest one had the listing agent blow a gasket and shriek at the buyer’s agent. This particular Clarkston house was listed as a 1974 home but none of the features matched the vintage. The attic was sheathed with dimensional wood, the attic framing was 2x4 rafters, the number of outlets was low, the foundation system was funky. It didn’t feel like 1974.
When the buyer’s rep showed up, I asked her about this. She commented that the seller had put a 1955 date in the disclosures. I ran with that and suggested a video sewer scope of the main drainage line. As it happens, the material was Orangeburg pipe and was in lousy condition. Given the extreme over-reaction of the listing agent, I wonder if she already knew that the line was questionable. Hmmmm?
Anyway, to the point. How does this happen? How does an old house get listed as a newer home?
The answer is not that the real estate agent is deliberately deceptive (usually!) What happens is that the house undergoes a major remodel, so much so that the home is nearly new in a functional sense. The owner applies for, and gets, a new certificate of occupancy from the municipality. The records get updated with the new C.O. When the house gets listed again, anyone (or any computer algorithm) will locate the last certificate of occupancy and that date gets assigned to listing.
This is not a 1974 attic space even though that was the listed age of the home.
The only time we used to see this happen was when a home was moved. With tighter controls coming into play at the municipal level, I expect to see more of this sort of mischaracterization occurring. The home inspector community will need to be aware of the potential for the actual vintage of the building to be different from the documentation. Unfortunately, with so many new inspectors arriving on the scene that lack the thousands of houses of experience to recognize the oddities, this likely will get missed.
Wait - Your Inspector Didn't Say Anything About Anchor Bolts?
First, a little history lesson. We tend to think that modern standards are inherently superior to the ‘good old days’. That may be so, but that does not mean that an older foundation is unsafe or needs a full retrofit. Many of our old foundations (in this region) are doing just fine. Many of those do not have a single anchor bolt, either.
Washington State began requiring anchor bolts on a statewide basis in about 1973 though many of our 1950s and 1960s Pullman and Clarkston homes have them. Prior to that, the state mandated them in the Puget Sound region due to earthquake potential.
Anchor bolting is installed to handle seismic and wind forces that have the potential to knock a home off the foundation. The Northridge quake is a case in point. The manner in which we installed them changed after that quake and the design of the washers was modified to limit damage.
Anchor bolts are not always visible - finished basement will prevent access - but it pays to have your inspector making the effort to identity if they are present or not. I do so in my reports on a separate line. If they are missing, the client gets a nice explanatory paragraph.
It’s a fairly common defect to find that the anchor bolts are present but missing washers and nuts. When this happens, it becomes a repair issue. If they are not spaced correctly, it becomes a judgement call - is it worth the cost to retrofit versus the risk. On this side of the state, our earthquake risk is minimal compared to Seattle. Most people don’t retrofit, but they always appreciate the information.
Don't Make Excuses
I am loathe to make excuses for why I couldn’t accomplish my job though it does happen. The 2016-2017 winter was so brutal that I didn’t climb a roof for two months. This year’s more mild winter has been much easier to deal with - but there are still occasions where your inspector has to extend some effort.
Garage Door Safety Sensors - What Height?
Little things count, too. There is actually a standard on the height of the sensor at the garage door and for good reason - set the sensor too far up and a small child can be caught under the door even with an otherwise fully operational safety system.
So, what is the maximum height?
6 inches.
Is Your Inspector Supposed to Remove the Cover on the Electrical Panel?
Per Washington State Standard of Practice, your home inspector is obligated to remove the cover from the electrical panel. This was a point of contention early in the standards-writing process and electrical contractors in particular argued against it.
Common sense prevailed and home inspectors remove covers. This is a necessary part of the inspection. Just in the last few days, I've seen a panel where the plastic was literally melting. (Yes, we turned off the power, notified the agent, and thanked our lucky stars the home didn't burn down the day before.)
We look for a variety of issues on the interior and I'll hit those in later posts and videos - though if you have a specific question, send it along and I'll move it up the queue.
One caveat - we are required to remove 'readily accessible' covers. If the panel is buried under behind a 700 lb. gun safe, I'm not inspecting it. Likewise, I add the very sensible (to me) proviso that if I test the panel and it lights me up, I'm not going further and trying to remove the cover. In either case, your inspector is obliged to tell you that he did not remove the cover and why.
Pullman Air Quality Is Terrible Today (8/20/18)
This happens every three or four years. We're surrounded by forests to our south and west and forests, by their nature, tend to burn after lightning strikes.
The air quality in Pullman is rated at very unsafe today. In Clarkston, it's even worse and has hit hazardous. For those of you who have central air systems but no air conditioner, you can put the fan into the "ON" mode to filter your air. If you have a/c, you can do this so the air is constantly filtered, but you're not paying to cool things down when you don't need to.
Be careful with all your outside activities. If you have folks (children or the elderly) with respiratory issues, keep an eye on them. Asthma sufferers (like me) should use their inhalers early.
Take care, everyone, and be safe. Send some prayers or kind thoughts, as your preference may be, to the firefighters working to save homes and our forests.
Angie's List Super Service Award Winner
If you look to the right-hand side of the front page, you will notice that I have a new award. In my first year with Angie's List, Safe@Home Inspections won their prized Super Service Award for 2017.
These are the sorts of things that happen by accident. It requires an enormous investment in giving my clients an outstanding inspection along with great service before and after the inspection.
Personally, I'm incredibly pleased. I'm also looking for ways to do even better this year.
My thanks to all the clients and their agents that placed their trust in me!
Building Permit Research
Curious if the home you are considering purchasing has a Certificate of Occupancy?
One of my clients was, on a relatively new (six year-old) custom home, and took the time to go down to the local Building Department to do the research. To the surprise of both of us, a CO had never been issued on the home. Since I had already referred him to a structural engineer due some very odd cracking and bowing in the walls, this was the final straw in the deal.
That was a couple of weeks ago. This past week, while resolving a disagreement on electrical bonding with a contractor, I discovered that another home that I had recently inspected never had a permit purchased or an inspection performed on a brand new roof.
If home inspections were done to the same standard as a commercial inspection, visiting the Building Department for document research would be automatic. Not so for home inspections.
Maybe that should change.
I'm am now including an add-on service for residential inspections. For $125.00, I will gather the available relevant documents including permit applications, inspection reports, and Certificates of Occupancy and deliver them to you as a .pdf file.
I am recommending this for homes 25 years old and older, homes reported to have been recently remodeled, and custom built homes. The reasoning is that it takes some time in the house's lifecycle to get to the remodel and retrofit phase. Roofs and mechanical equipment usually do not need change-out earlier. Remodels trigger their own permit requirements. Custom homes fall across a broad spectrum of professional competencies. In the case above, the builder went out of business, leaving the current owner in a major lurch.
I do not recommend it for spec-built homes. Companies such as Copper Basin and Hayden Homes are consistent about acquiring the necessary permits. They are too big to fly under the radar for the Building Departments.
A minimum of three business notice required.
Railroad tie retaining walls
In Pullman and Moscow both, a ‘natural-look’ trend using railroad tie retaining walls took place from the mid-1980’s to about 2000, when masonry block supplanted the trend. The advantage of the railroad ties was the number of them dropped onto the market as local rail lines got torn up and the creosoted wood was nearly given away.
As is usually the case, the contractors that first started using the ties had no idea of what a wall constructed of wood should look like. Mostly, they pretended that it was just like a concrete wall. They stacked the ties, drove spikes through them vertically and—viola’—counted it as good.
It wasn’t. The railroad ties are prone to rotating and the spikes aren’t enough to resist the motion. Add to that the ground pressure, especially when the native loess around here gets wet, and the retaining walls tend to pick up a lean pretty quickly.
There’s a way to fix the issue, though. At the time you build the wall, you include tiebacks. Tiebacks can be made with steel rods and use anchor bolts to flat plates at the outside of the wall. A more attractive solution that works equally well is to use the railroad ties themselves as the tiebacks by turning an appropriate number of them perpendicular to the wall, extending into the hillside you are retaining.
If you look at the railroad tie retaining wall in the picture, you can see a tieback in the lower middle part of the picture where the end profile of the tie is visible.
No, I can’t tell you the appropriate number of tiebacks – that is known as engineering and I’m not qualified. As an inspector, I recognize when this has been done (and hasn’t, obviously) and point it out to the client.
Now, for the other problem with using railroad ties in retaining walls, at least in Pullman and Moscow—the ties are a multi-story hotel for carpenter ants.
The creosote coating will keep them from penetrating the surface of the wood but any cut ends or sections that split will provide an entry point. Once inside, the carpenter ants will set up house. Unlike most other wood destroying organisms in the Pacific Northwest, the ants don’t eat the wood. They excavate and create shelters.
While their presence in the wall will weaken it, they’re not yet a threat to your home until they attempt to colonize it in the same manner they took over the railroad ties. As part of a home inspection in Washington State, the inspector is required to inform you of potential conditions conducive to this type of infestation. Note the difference . . . potential. Just because the condition exists, it does not automatically follow that an infestation is imminent.
It would be prudent to have a professional keep an eye on the potential for you and, if it’s a concern, provide treatment options. A pair of companies I like are Sunpest and Hayden Pest Control. {Disclaimer-Sunpest helps me with my dandelion issues.}
Railroad tie retaining walls are an attractive landscaping feature but, when buying a new home, look for the signs (or make sure your inspector looks) of good construction and be mindful of the pest issues. Otherwise, enjoy the natural beauty they bring.
Cracked Heat Exchangers
Cracked heat exchangers are not just expensive - they can be dangerous as hell. First, background. A gas-fired furnace (oil, too) has two different air-handling systems. The one most people think about is the blower that moves that wonderful warm air through the house on days where the temps, like today, are in the single digits.
The second system is the air supply for the burning of the gas. The furnace needs this air for combustion. The resulting flue gases are a mix of the air, minus a goodly portion of oxygen, and the fuel, minus a goodly portion of the chemical energy. That's where the heat comes from.
To get it into the house, we need to move the heat from the combustion cycle to the air-handling equipment. That's the role that the heat exchanger plays. It's a shell of metal that contains the noxious gases of combustion. The walls of the exchanger heat up and transfer the heat to the air driven by the blower.
The old furnaces from the 1960's and early 70's had thick shells and some of those old Lennox's can be hard to kill with anything short of a bazooka. Newer furnaces, especially the ultra-high efficiency condensing furnaces, don't last nearly as long. The new ones have much thinner shells and, to create greater surface area for the heat transfer, lots of dimples in the surface. Consequently, they tend to suffer metal fatigue faster than the old furnaces. Failures in heat exchangers have been reported in units that are only 15 years old.
Back to the noxious gases. What happens when the heat exchanger cracks? Well, we no longer have a separation between the gases and our interior air, the atmosphere that we breathe. The flue gases escape into the living spaces. The principal gas? Carbon monoxide.
The reading on my handy little toy there indicates that the furnace is releasing 16 parts per million of carbon monoxide. As a reference, at levels above 9 parts per million, carbon monoxide begins to affect health. At 35 parts per million, it becomes toxic. These are based on 8 hour exposure cycles, about the amount of time you spend (hopefully) sleeping.
There are a couple of things that you can do to protect yourself. First, have the furnace serviced on a regular basis and make sure you specify that the heat exchanger is inspected for cracks. While you would think that it would be routine, my experience in this area is that it isn't.
Second, install carbon monoxide detectors. They are relatively inexpensive. In older homes, it is perfectly acceptable to use either the plug-in type or ceiling mounted battery operated detectors. In newer homes in Washington State, they are required to be hard-wired into the home.
A special note for people selling homes in Washington State - you are legally required to furnish the home with detectors when you sell your home. This applies even if you are doing it as a for-sale-by-owner (FSBO).
If you are a buyer, I strongly recommend asking the inspector if he uses a carbon monoxide detector during his inspection. They're not foolproof - even if I get acceptable readings on mine, I'll request the heat exchanger be checked by an HVAC specialist - but they are very useful. A good inspector should have one.
Finally, what can be done about cracked heat exchangers? Replacement of the furnace, generally. That's the part that is expensive. It beats being one of the 500 people who die every year from CO poisoning, though.
Crawl Space Access
Crawl space access is one of those completely unsexy things that inspectors get excited about - and with good reason, since we get paid to go in there. Most homebuyers take one look at the spider webs and confined space and pat me on the back. "Good luck, take pictures." seems to the general idea. They're not coming with me. Accesses get placed in all sorts of interesting spots - outside, in the garage, through a basement wall, closets - you name it, someone has put it there.
Okay, not the attic. We'll save the discussion of attic scuttles for another time. . .
The code for crawl space access is pretty specific.
R408.4 Access Access shall be provided to all under-floor spaces. Access openings through the floor shall be a minimum of 18 inches by 24 inches (457 mm by 610 mm). Openings through a perimeter wall shall be not less than 16 inches by 24 inches (407 mm x 610 mm). When any portion of the through-wall access is below grade, an areaway not less than 16 inches by 24 inches (407 mm x 610 mm) shall be provided. The bottom of the areaway shall be below the threshold of the access opening. Through wall access openings shall not be located under a door to the residence.
Did you read all that? No, don't worry. The inspector will manage it. Heck, we're delighted if we actually get a code-compliant hatch in an older home. Some that I've gone through are a half or less of the size above. It's why you should always hire a skinny inspector.
No, the part that will drive the inspector nuts and possibly cost you money (if you're the buyer) or a sale (if you're the seller) is having a perfectly acceptable hatch that isn't accessible.
Don't Cover or Block the Crawl Space Access
Yesterday was a classic example. We have a home with a sloped floor, a large tree five feet from the foundation wall, and no way to check the crawlspace for structural damage because the hatch was in the laundry room. Under the washer/dryer.
Very few inspectors are going to move installed appliances, risking damage to the appliances and the flooring, to get to a hatch. Instead, most will write it up as a defect, mark the structural components as uninspected and leave the buyer guessing about sloped floors.
The longer they guess, the worse the problem will get in their minds.
If you are the seller, please do yourself a favor. First, know where your access is. If it's under equipment, take the time to move things for the inspector.
If it's in a closet, remove your personal possessions to leave it available. Same thing for exterior hatches - don't stack the firewood on top.
Some older homes will have the hatch nailed down. If this is the case, pry it up before the inspector gets there. The odds are that he or she won't take the chance of damaging flooring.
And if you're using screws to hold the covers in place - frequently done on exterior hatches to keep the board tight to the wall - use a standards screw head - no need to go with fancy star-patterned heads. We might not have that particular pattern or size on board the truck. Use a Phillips or square head screw.
The inspector will thank you, and the buyer will get the information they need without the extra worrying. And you move one step closer to a successful sale.
EPA Bans Most Wood-Burning Stoves
Well, it's not like we're not used to the EPA overreaching on regulations so a production ban on the types of wood-burning stoves found in about 80 percent of the homes nationwide with stoves shouldn't be a surprise. The core of the issue is a requirement that wood stoves produce less than 12 micrograms per cubic meter of air of airborne fine-particle matter. The old standard was 15 percent.
You can still use your old wood stove - for now, and depending on region - but if you want to get a new stove, the old one will need to be scrapped out. You can't sell it to another party to recoup some of your outlay for the more efficient burner. I also suspect that the new regulations will increase the cost of the new wood-burning stoves as well though the EPA helpfully provides a list of compliant stoves.
Some areas of the country already ban outright the use of a wood stove during certain weather conditions or seasonally. Puget Sound and the Air Resources Board in that region have done that.
If you are buying a home with a wood stove, I would strongly suggest finding out if the stove is compliant. As an inspector, this isn't going to be part of my routine since there is too great a variety in the stoves themselves. Also, I would keep in mind the fact that the stove that you have may be banned from use should the local jurisdictions decide that it is necessary. Such bans almost invariably involve the traditional fireplace as well.
If you are a seller with a new wood-burning stove that is EPA compliant, I would include that information in the listing. Discuss it with your Realtor to see how best to do this.
For more info, here's the article that I found - EPA Bans Most Wood-Burning Stoves
Gas Log Fireplace Maintenance
The next time you snuggle up near the warmth of a gas fireplace, ask yourself when the last time you had someone do maintenance on it. Usually ignored, gas log fireplace maintenance should be done annually just as you do with your furnace. Right, the furnace is do, too, but that's a different post.
Regular Cleaning
Most of the manufacturers of gas log fireplaces and inserts recommend having the system serviced on an annual basis. Most of this you can accomplish on your own if you are reasonably handy. Always remember to turn off the pilot and the gas to the fireplace before working on it.
Use a brush to clean the control space and the burner once you have the unit opened up. Use a very soft bristle brush to clean the logs - they tend to be fragile, so handle with some care.
Some logs, called 'yellow flame logs', require more frequent maintenance. They don't generate as much heat as the blue flamed logs but present an attractive appearance that rivals a traditional wood fire. The yellow color of the flame is a result of the carbon in the logs and, like the wood-burning fireplace, generates soot. Chimneys for these require the same maintenance as the traditional chimney.
The glass can be cleaned with a standard glass cleaner. Be careful with trim work and clean only with a damp rag - using chemicals might etch the finishes and ruin the appearance of the fireplace.
The Vent
Before you start the fireplace for the first time, check to make sure that the vent is clear of debris and dead animals. Also verify that there are no cracks or holes in the flue pipes. Check for condensation the first time you ignite the fireplace. There will be a little bit but it should burn off quickly. If it doesn't, the condensation may combine with the combustion gases and make a weak corrosive solution that can attack the metal of the flue.
Call the Pros!
The manufacturer also recommends annual service of the gas log fireplace by trained professionals. You really do need to have them come out to service the system. While you can clean and maintain the burner components and do a routine inspection of the vents, the pros can check the fuel/air mixture to make sure that the fireplace operates at optimum efficiency, check for gas leaks, and inspect the blower components to ensure the fan operates correctly.
A reminder - if you smell gas, call a service person immediately and describe to them the type and strength of the odor. Follow their instructions - if they say get out - Get Out!
A second reminder - install a carbon monoxide detector even if everything else in your house is electric. Any home with a gas-fired or wood-burning fireplace or furnace should have one.
So, the basics of gas log fireplace maintenance. Do it and enjoy the ambience all winter, worry-free.
Ufer Ground for New Construction
The term ufer ground is the old fashioned way to call out what the code book calls a concrete-encased grounding electrode. You probably don't know it but most new homes in the Pullman and Moscow areas are being built with a Ufer ground. First, let's have a short history lesson. In World War II, the American forces, specifically the U.S. Army, needed a system to ground bomb storage facilities in Arizona and Nevada. One problem with both of those areas is that they are extremely dry and the soil was a very poor conductor. For obvious reasons, the Army did not want excessive charges to build up around the bomb dumps. The existing means - long copper rods - would take a critical war material our of circulation and was very expensive.
Fixing this problem was Herbert G. Ufer. A sharp individual, he discovered that the foundations, made of concrete, were more conductive than many types of soil. He devised a system by which a rod was inserted into the foundation and tied to the electrical panel.
Moving on....
The concrete encased grounding electrode used in our region for residential construction is a 20 foot length of #4 rebar (1/2 inch steel) with a projection from the top of the foundation wall at a easy location to make the connection to the grounding electrode - the actual wire from the panel.
The old means - there were two - of grounding proved to be less effective in Pullman and Moscow due to better knowledge and a change in building material.
The early means of grounding was to attach the grounding electrode to the metal plumbing system where the main entered the home. Now that we use non-metallic materials for our plumbing supplies, this option isn't available.
The other way was to use driven ground rods. Unfortunately, these were less proficient at distributing energy and were often damaged at the clamps that held the wire to the rod.
How to determine if you have a Ufer Ground? Look inside the home under the electrical panel. What you are trying to find is a blank electrical box cover plate. If you have one and can not find a ground rod outside, there is a good chance that you have a ufer ground. The plate is there, by the way, in case you do have a major electrical event and the connection to the rod needs to be checked for damage.
Now a word of warning - nothing ever comes without a downside. Ufer grounds have been known, under certain conditions, to cause damage to the foundation in a lightning strike. If the concrete holds too much moisture, that water will flash off to steam and the expansion of the steam cracks the concrete.
Make sure that you keep your gutters in good shape and, when you water the lawn, make sure you're not watering the house, too. It's not good for the house and it can be a problem - not a high probability one, admittedly, but possible - for your ufer ground system.
Radon Re-test
First thing this morning I have a stop in Pullman to set up radon re-test - follow-up radon testing as recommended by the EPA. The first test gave us a result right at the action level of 4.0 pCu/L and we want to make sure that we have a good number. Since the testing is done by sampling, a small statistical bias can enter into the results, hence the retest fro radon gas.
We're also running a longer test which will give us a smoother data set.
And, since I always offer a free radon follow-up test if the clients wants it, this test is free.
Washington State License #215
Former SBCC Member, Former Chairman State Home Inspector Advisory Licensing Board.