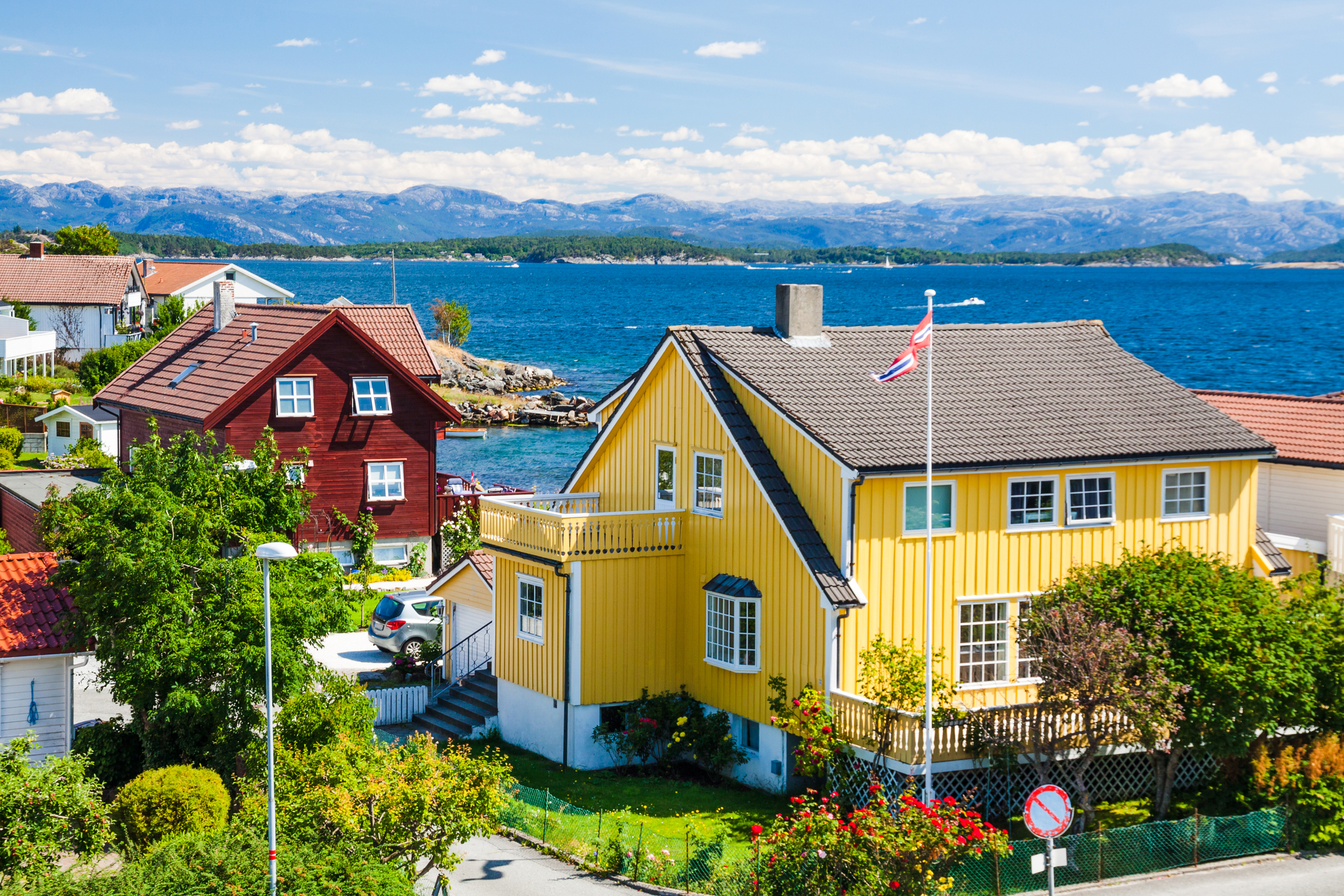
Is Your Inspector Supposed to Remove the Cover on the Electrical Panel?
Per Washington State Standard of Practice, your home inspector is obligated to remove the cover from the electrical panel. This was a point of contention early in the standards-writing process and electrical contractors in particular argued against it.
Common sense prevailed and home inspectors remove covers. This is a necessary part of the inspection. Just in the last few days, I've seen a panel where the plastic was literally melting. (Yes, we turned off the power, notified the agent, and thanked our lucky stars the home didn't burn down the day before.)
We look for a variety of issues on the interior and I'll hit those in later posts and videos - though if you have a specific question, send it along and I'll move it up the queue.
One caveat - we are required to remove 'readily accessible' covers. If the panel is buried under behind a 700 lb. gun safe, I'm not inspecting it. Likewise, I add the very sensible (to me) proviso that if I test the panel and it lights me up, I'm not going further and trying to remove the cover. In either case, your inspector is obliged to tell you that he did not remove the cover and why.
Ufer Ground for New Construction
The term ufer ground is the old fashioned way to call out what the code book calls a concrete-encased grounding electrode. You probably don't know it but most new homes in the Pullman and Moscow areas are being built with a Ufer ground. First, let's have a short history lesson. In World War II, the American forces, specifically the U.S. Army, needed a system to ground bomb storage facilities in Arizona and Nevada. One problem with both of those areas is that they are extremely dry and the soil was a very poor conductor. For obvious reasons, the Army did not want excessive charges to build up around the bomb dumps. The existing means - long copper rods - would take a critical war material our of circulation and was very expensive.
Fixing this problem was Herbert G. Ufer. A sharp individual, he discovered that the foundations, made of concrete, were more conductive than many types of soil. He devised a system by which a rod was inserted into the foundation and tied to the electrical panel.
Moving on....
The concrete encased grounding electrode used in our region for residential construction is a 20 foot length of #4 rebar (1/2 inch steel) with a projection from the top of the foundation wall at a easy location to make the connection to the grounding electrode - the actual wire from the panel.
The old means - there were two - of grounding proved to be less effective in Pullman and Moscow due to better knowledge and a change in building material.
The early means of grounding was to attach the grounding electrode to the metal plumbing system where the main entered the home. Now that we use non-metallic materials for our plumbing supplies, this option isn't available.
The other way was to use driven ground rods. Unfortunately, these were less proficient at distributing energy and were often damaged at the clamps that held the wire to the rod.
How to determine if you have a Ufer Ground? Look inside the home under the electrical panel. What you are trying to find is a blank electrical box cover plate. If you have one and can not find a ground rod outside, there is a good chance that you have a ufer ground. The plate is there, by the way, in case you do have a major electrical event and the connection to the rod needs to be checked for damage.
Now a word of warning - nothing ever comes without a downside. Ufer grounds have been known, under certain conditions, to cause damage to the foundation in a lightning strike. If the concrete holds too much moisture, that water will flash off to steam and the expansion of the steam cracks the concrete.
Make sure that you keep your gutters in good shape and, when you water the lawn, make sure you're not watering the house, too. It's not good for the house and it can be a problem - not a high probability one, admittedly, but possible - for your ufer ground system.
Washington State License #215
Former SBCC Member, Former Chairman State Home Inspector Advisory Licensing Board.